High-Density Interconnect (HDI) boards have revolutionized the field of Printed Circuit Board Assembly (PCBA) by enabling compact designs and improved performance for electronic devices. These advanced PCBs support higher component density, reduced signal loss, and faster signal transmission, making them indispensable for applications like smartphones, medical devices, automotive systems, and advanced computing. However, achieving high-performance PCBA with HDI boards requires meticulous planning, precise execution, and leveraging advanced manufacturing technologies. Below, we outline actionable strategies and insights from professional complex PCB manufacturers.
1. Understanding HDI Board Design Fundamentals
A well-executed HDI PCBA begins with an optimized design. The layout of an HDI board is inherently more complex than standard PCBs due to the use of fine traces, microvias, and multiple layers. Here are key considerations for effective HDI board design:
- Layer Stack-Up Configuration: Choosing the right layer stack-up is critical for maintaining signal integrity and reducing electromagnetic interference (EMI). A balanced stack-up minimizes warping during assembly.
- Via Types and Placement: HDI boards use blind, buried, and microvias to connect layers. Manufacturers should strategically place these vias to optimize routing and minimize space consumption.
- Trace Width and Spacing: Adhering to the appropriate design rules for trace width and spacing is essential to prevent crosstalk and ensure reliable signal transmission.
- Design for Manufacturability (DFM): Collaborating with manufacturers during the design phase ensures that the HDI board’s features align with fabrication and assembly capabilities.
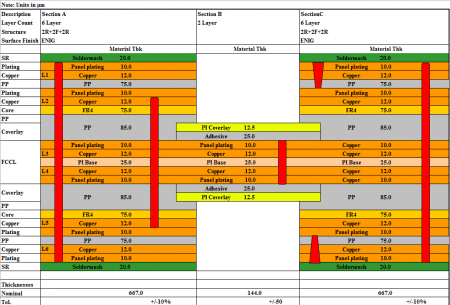
2. Selecting High-Quality Materials
The performance and reliability of an HDI board significantly depend on the materials used in its fabrication. Professional PCB manufacturers recommend:
- Low-Loss Dielectrics: Use materials with low dielectric constant (Dk) and low dissipation factor (Df) to minimize signal loss and maintain high-speed performance.
- High-Temperature Substrates: For applications requiring thermal resilience, choose materials with high glass transition temperatures (Tg).
- Copper Foils and Laminates: Opt for copper foils with excellent conductivity and laminates that can withstand the rigors of HDI manufacturing processes.
3. Leveraging Advanced Manufacturing Technologies
HDI PCB fabrication involves sophisticated processes that demand precision and expertise. Key technologies include:
- Laser Drilling for Microvias: Laser drilling ensures precise microvia creation, which is essential for achieving compact designs and high signal integrity.
- Sequential Lamination: This process involves building up the PCB layer by layer, allowing for the incorporation of advanced features such as stacked or staggered vias.
- Advanced Plating Techniques: High-quality plating ensures reliable electrical connections and enhances the board’s durability.
- Automated Optical Inspection (AOI): AOI systems detect defects early in the manufacturing process, ensuring the final product meets stringent quality standards.
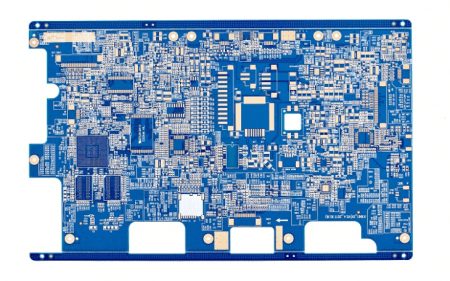
4. Optimizing Assembly Processes
The assembly stage is where components are mounted onto the HDI board, and its success depends on:
- Precise Solder Paste Application: Use high-precision stencil printing or jet printing for solder paste application to accommodate the fine pitch of HDI components.
- Advanced Pick-and-Place Machines: Employ machines capable of handling micro-components and ensuring accurate placement.
- Reflow Soldering Profiles: Develop reflow profiles tailored to the thermal properties of the board and components to prevent warping or damage.
- Inspection and Testing: Conduct thorough inspection using X-ray and AOI systems to identify and rectify defects such as solder bridges, voids, or misaligned components.
5. Collaborating with Experienced Manufacturers
Partnering with a professional HDI PCB manufacturer can significantly enhance your PCBA performance. Such manufacturers bring:
- Expert Design Assistance: Their experience helps in refining designs for optimal manufacturability and performance.
- State-of-the-Art Facilities: Advanced equipment and cleanroom environments ensure the precision required for HDI boards.
- Comprehensive Testing: From in-circuit testing (ICT) to functional testing, these manufacturers ensure your board meets rigorous quality and performance standards.
- Custom Solutions: Experienced manufacturers can tailor solutions to specific industry needs, whether for aerospace, medical, or consumer electronics applications.
6. Ensuring Long-Term Reliability
For HDI boards used in critical applications, reliability is non-negotiable. To ensure long-term performance:
- Implement Robust Quality Control: Adhere to international standards such as IPC-6012 and ISO certifications.
- Perform Environmental Testing: Subject the boards to thermal cycling, humidity exposure, and vibration testing to validate their durability.
- Adopt Conformal Coating: Apply conformal coatings to protect against environmental factors like moisture, dust, and chemical exposure.
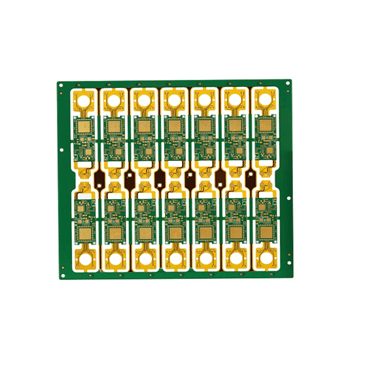
12 layer HDI PCB prototype
Conclusion
High-performance PCBA with HDI boards requires a synergistic approach encompassing design optimization, material selection, advanced manufacturing, and rigorous testing. By following these strategies and collaborating with professional complex PCB manufacturers, you can achieve superior functionality, reliability, and miniaturization in your electronic devices. As technology evolves, HDI boards will continue to play a pivotal role in driving innovation across industries. Embrace these insights to stay ahead in the competitive landscape.
XPCB Limited: Your One-Stop Solution for PCB Manufacturing and Assembly
XPCB Limited is your one-stop solution for all your PCB manufacturing and assembly needs. From design and prototyping to full-scale production, we offer comprehensive services under one roof. With a focus on quality, efficiency, and customer satisfaction, we make it easy for you to complete your projects with confidence. Simplify your PCB process today with XPCB Limited.