The automotive industry has long been a hotbed for technological innovation, with advancements in materials, engineering, and electronics shaping the vehicles of today. Among these advancements, flexible printed circuit boards (flex PCBs) have emerged as a pivotal technology, enabling new possibilities in design, functionality, and reliability. By integrating flexibility and durability, flex PCBs are redefining how automotive electronics are designed and implemented.
What Are Flex PCBs?
Flex PCBs are circuit boards designed to bend, twist, and conform to complex shapes without compromising functionality. Unlike rigid PCBs, which are limited by their inflexibility, flex PCBs are made using flexible substrates such as polyimide or polyester films. This adaptability allows them to be used in tight spaces and unconventional geometries, making them ideal for modern automotive applications.
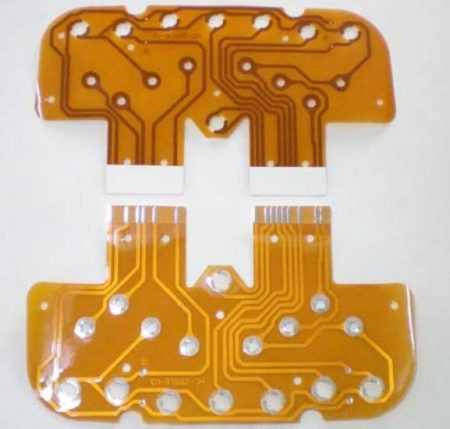
The Growing Role of Flex PCBs in Automotive Electronics
Flex PCBs have revolutionized various aspects of automotive electronics, becoming indispensable in:
- Advanced Driver-Assistance Systems (ADAS)
- Flex PCBs support the sophisticated electronics required for ADAS, including cameras, radar sensors, and LiDAR systems. Their flexibility enables seamless integration into curved surfaces and confined spaces.
- In-Vehicle Infotainment Systems
- From touchscreen displays to advanced audio systems, flex PCBs are crucial in delivering high-quality, compact, and reliable infotainment solutions.
- Electric Vehicles (EVs)
- The transition to EVs has increased the demand for lightweight and energy-efficient components. Flex PCBs contribute to weight reduction while ensuring robust electrical connections in battery management systems and motor controllers.
- Lighting Systems
- Modern LED and adaptive lighting systems in automobiles often require intricate circuits that fit within limited spaces. Flex PCBs make it possible to achieve these designs with ease.
Advantages of Flex PCBs in Automotive Applications
The unique properties of flex PCBs offer numerous advantages:
- Space Optimization
- Flex PCBs can be folded or curved, allowing designers to maximize the use of available space in compact areas such as dashboards and engine compartments.
- Durability and Reliability
- Automotive environments expose components to vibrations, extreme temperatures, and mechanical stress. Flex PCBs are designed to withstand these conditions, ensuring long-term reliability.
- Weight Reduction
- By eliminating bulky connectors and cables, flex PCBs help reduce the overall weight of automotive systems, improving fuel efficiency and performance.
- Design Flexibility
- Flex PCBs enable innovative designs that were previously unattainable with traditional rigid PCBs. This opens up opportunities for new aesthetic and functional features in vehicles.
- Cost Efficiency
- Despite higher initial production costs, flex PCBs often lead to cost savings by simplifying assembly processes and reducing the need for additional connectors and components.
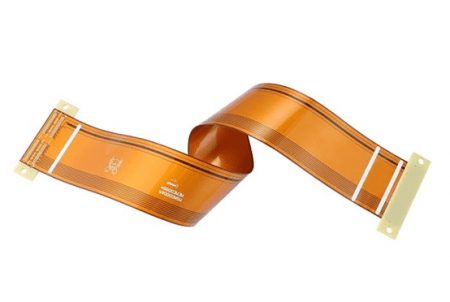
Challenges in Implementing Flex PCBs in Automotive Electronics
While flex PCBs offer transformative benefits, their implementation is not without challenges:
- Complex Manufacturing Processes
- The production of flex PCBs requires specialized equipment and techniques, leading to higher upfront costs and longer lead times.
- Material Limitations
- Selecting materials that can withstand automotive conditions while maintaining flexibility is critical. Issues such as thermal expansion and mechanical stress must be carefully addressed.
- Design Expertise
- Designing circuits that take full advantage of the flexibility of flex PCBs requires advanced engineering expertise and collaboration between designers and manufacturers.
The Future of Flex PCBs in Automotive Electronics
As the automotive industry moves toward autonomous vehicles and enhanced connectivity, the role of flex PCBs will continue to expand. Key trends shaping the future include:
- Integration with IoT and Connectivity
- Flex PCBs will play a vital role in enabling vehicle-to-everything (V2X) communication systems, ensuring seamless connectivity in smart transportation networks.
- Miniaturization of Components
- The demand for smaller and more efficient components will drive further innovation in flex PCB design and materials.
- Sustainability Initiatives
- With increasing emphasis on eco-friendly designs, flex PCBs will contribute to lightweight and energy-efficient solutions, aligning with global sustainability goals.
- Advancements in Manufacturing Technologies
- Emerging techniques such as additive manufacturing and laser processing are expected to reduce production costs and enhance the capabilities of flex PCBs.
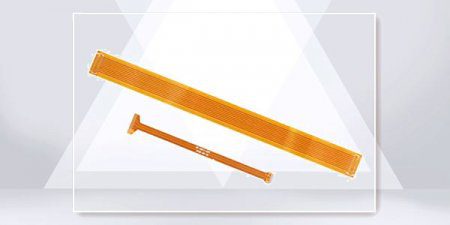
Conclusion
Flex PCBs are undeniably a game-changer in automotive electronics, enabling groundbreaking advancements in design, functionality, and performance. By addressing the challenges and leveraging emerging technologies, the automotive industry can fully harness the potential of flex PCBs to create vehicles that are smarter, safer, and more efficient.
As the industry continues to innovate, the integration of flex PCBs will not only meet the demands of today but also set the stage for the vehicles of the future. For manufacturers, engineers, and designers, embracing this technology is essential to staying competitive in an increasingly connected and electrified world.
Advanced PCB Manufacturing and Quick-Turnaround Prototyping by XPCB Limited
XPCB Limited specializes in delivering advanced PCB manufacturing combined with quick-turnaround prototyping to meet the demands of your most time-sensitive projects. With cutting-edge technology and a commitment to precision, we provide exceptional PCB solutions tailored to your specifications. Trust XPCB Limited to help you accelerate your development cycle without compromising on quality.