In the fast-paced evolution of automotive technology, electronic systems play a pivotal role in redefining how vehicles operate and interact with their environment. From autonomous driving and advanced driver-assistance systems (ADAS) to cutting-edge infotainment setups, the integration of sophisticated electronic systems is revolutionizing the automotive landscape. At the core of these advancements lies a critical enabler: Rigid-Flex PCBs (Printed Circuit Boards).
This blog delves into how rigid-flex PCBs are driving innovation in modern automotive electronics, their unique features, benefits, applications, and future potential.
The Growing Importance of PCBs in Automotive Systems
Automotive systems today are significantly more complex than ever before. Vehicles are equipped with a plethora of electronics that demand compact, lightweight, and highly reliable solutions. This trend is particularly pronounced in:
- Autonomous Vehicles: Sensors, cameras, LiDAR, and radar systems form the backbone of autonomous driving technologies.
- Electric Vehicles (EVs): Battery management systems (BMS), inverters, and charging modules rely heavily on advanced PCB technologies.
- ADAS: Features like lane-keeping assist, adaptive cruise control, and collision avoidance depend on robust electronic systems.
- Infotainment Systems: Seamless connectivity, advanced displays, and audio systems demand high-speed, compact circuits.
Rigid-flex PCBs meet the requirements of these applications by offering unparalleled reliability, adaptability, and efficiency.
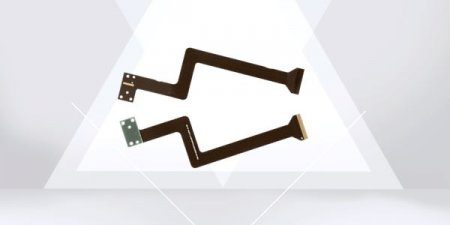
What Are Rigid-Flex PCBs?
Rigid-flex PCBs combine the structural support of rigid boards with the flexibility of flexible circuits into a single, integrated solution. These hybrid boards consist of multiple layers of flexible substrates attached to rigid sections, enabling innovative designs that would be challenging or impossible with traditional PCBs.
Key Features of Rigid-Flex PCBs:
- Durability: Withstand harsh automotive conditions, including vibrations, extreme temperatures, and humidity.
- Compact Design: Enable space-saving and lightweight configurations by reducing connectors and cables.
- High Signal Integrity: Minimize signal loss and electromagnetic interference (EMI).
- Flexibility: Allow for bending and folding, crucial for confined spaces in automotive electronics.
Advantages of Rigid-Flex PCBs in Automotive Applications
- Space and Weight Savings
Traditional PCBs often require extensive wiring and connectors, which increase weight and occupy valuable space. Rigid-flex PCBs streamline designs, providing compact and lightweight solutions ideal for modern vehicles.
- Enhanced Durability
Automotive environments subject electronic components to constant stress from vibration, heat, and moisture. Rigid-flex PCBs are designed to endure these conditions, ensuring reliability and longevity.
- Simplified Assembly
The integration of rigid and flexible sections reduces the number of components and simplifies assembly processes, leading to cost savings and improved efficiency.
- Improved Reliability
By eliminating multiple interconnections, rigid-flex PCBs reduce potential points of failure, ensuring robust performance for critical automotive systems.
- Greater Design Flexibility
The ability to bend, twist, and fold rigid-flex PCBs opens up new possibilities for innovative designs that fit into unconventional spaces, such as curved dashboards and tight engine compartments.
Applications of Rigid-Flex PCBs in Automotive Electronics
- Advanced Driver-Assistance Systems (ADAS)
ADAS relies on a network of sensors, cameras, and control units to enhance vehicle safety and performance. Rigid-flex PCBs provide the reliability and compactness needed for these high-precision systems.
- Infotainment and Connectivity
The demand for high-speed data transmission, seamless connectivity, and advanced touchscreens has grown exponentially. Rigid-flex PCBs enable the integration of infotainment systems with minimal wiring and reduced EMI.
- Electric Vehicle Battery Management Systems (BMS)
BMS monitors and manages the performance of EV batteries. Rigid-flex PCBs offer the durability and efficiency required for these energy-critical systems.
- Lighting Systems
Automotive lighting, including LED headlights and ambient lighting, benefits from the flexibility and reliability of rigid-flex PCBs, which allow for creative designs and efficient power distribution.
- Autonomous Driving Technologies
Autonomous vehicles rely on interconnected systems for navigation, object detection, and decision-making. Rigid-flex PCBs ensure the seamless operation of these components in compact and challenging environments.
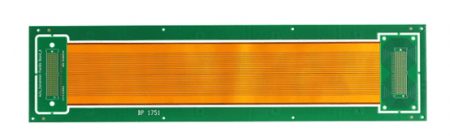
Challenges in Rigid-Flex PCB Adoption
While rigid-flex PCBs offer substantial benefits, they also pose certain challenges:
- Higher Initial Costs
The design and manufacturing of rigid-flex PCBs are more complex than traditional PCBs, leading to higher upfront costs. However, these costs are offset by long-term benefits, including reliability and reduced assembly complexity.
- Complex Design and Manufacturing Processes
Rigid-flex PCB designs require expertise in balancing rigid and flexible sections. Additionally, manufacturing processes demand precision to ensure optimal performance.
- Material Constraints
Selecting the right materials that offer flexibility, durability, and thermal resistance is critical but can limit design options.
The Future of Rigid-Flex PCBs in Automotive Electronics
The automotive industry is transitioning towards electrification, connectivity, and autonomy. This shift is expected to amplify the demand for rigid-flex PCBs due to their versatility and performance.
Emerging Trends:
- 3D PCB Designs: Advances in 3D PCB manufacturing will enable more complex and customized rigid-flex configurations.
- IoT-Enabled Vehicles: Connected cars will require sophisticated PCB solutions to integrate sensors, processors, and communication modules.
- Sustainability: The development of eco-friendly materials and recycling methods will make rigid-flex PCBs more sustainable.
- Improved Cost Efficiency: Innovations in production techniques are likely to reduce costs, making rigid-flex PCBs accessible for broader automotive applications.
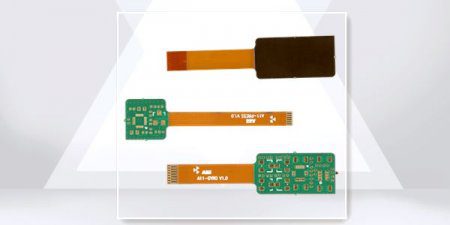
Conclusion
Rigid-flex PCBs are not just a technological advancement—they are the backbone of modern automotive electronics. Their unique combination of durability, flexibility, and efficiency is unlocking new possibilities for vehicle design and performance.
As the automotive industry continues to innovate, rigid-flex PCBs will remain at the forefront, driving progress in safety, efficiency, and connectivity. For manufacturers and designers, embracing rigid-flex PCB technology is essential to staying ahead in the race toward the future of mobility.
Advanced PCB Manufacturing and Quick-Turnaround Prototyping by XPCB Limited
XPCB Limited specializes in delivering advanced PCB manufacturing combined with quick-turnaround prototyping to meet the demands of your most time-sensitive projects. With cutting-edge technology and a commitment to precision, we provide exceptional PCB solutions tailored to your specifications. Trust XPCB Limited to help you accelerate your development cycle without compromising on quality.