Dimensional control of flexible circuits is an important aspect in the flex PCB manufacturing process to ensure that the final product meets the required specifications and functions properly. Flexible circuits are thin and flexible electronic circuits made up of flexible substrates, such as polyimide or polyester film, that can be bent or curved to fit into tight spaces or conform to irregular surfaces. The dimensional control of flexible circuits involves ensuring the accuracy and consistency of the circuit’s size, shape, and position of the components on the substrate.
The major flex PCB manufacturing steps for standard double-sided flexible circuits with through holes are listed here.
Each step should be considered carefully to determine its contribution to the overall distortion:
- NC drilling: Although NC drilling does not significantly impact the final dimension, certain scale factors based on assumed movements during the following operations may be factored into the drill pattern.
- Through-hole plating: Because the electric field in a through-hole plating bath is generally non-uniform, the copper thickness becomes uneven. An extremely thickly plated copper conductor will create mechanical stresses. During the etching process these stresses are released, generating some dimensional changes. In an extreme case, a copper-plated sheet cannot lie flat. An appropriate set of work fixtures and plating electrodes should be designed to create a uniform plating thickness.
- Dry film lamination and pattern printing: Due to the relatively low temperature and lack of wet processing (moisture), dry film lamination and pattern printing have little effect on dimensional control. Pattern imaging is, however, an opportunity to apply appropriate dimensional corrections for the following processes.
- Etching and stripping of resist: The most critical wet process in flexible circuit manufacturing is etching. Dimensional changes can occur when the by-products of the etching process are combined with the various materials. It is important to identify how to correct the various dimensional alterations, particularly as additional factors are incorporated into the process.
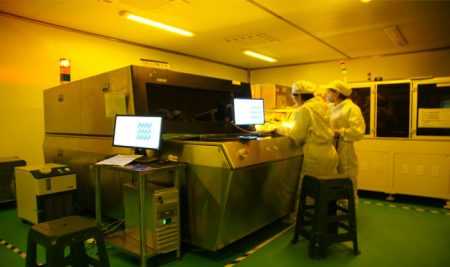
Image 1: Flex PCB manufacturing process
- Coverlay processes several overlay processes have been developed with varying process conditions for different concept materials. Film overlay undergoes a manufacturing process with a temperature greater than 160°C and a pressure over 20 kg/cm2. Cover coat ink withstands a screen-printing process with a drying temperature higher than 130°C. A newly developed photo imageable overlay must be baked at over 150°C. The majority of the heat and pressure processes impact dimensional stability significantly. Additional factors, such as press pad heating, make dimensional changes even more complicated. Conditioning should be reviewed in detail for each construction.
- Lamination pressing for multilayers Like the coverlay process, lamination pressing involves high temperature and pressure. Due to the number of layers, however, dimensional changes are more complicated because each level needs to be considered.
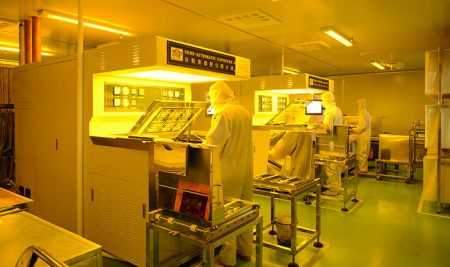
Image 2: Flexible Circuit Manufacturing
Some of the methods used for dimensional control of flexible circuits include:
- Design verification: Before manufacturing begins, the design of the flexible circuit is verified using computer-aided design (CAD) software to ensure that it meets the required specifications.
- Substrate selection: The selection of the substrate material is critical in ensuring dimensional stability as different materials have different thermal expansion coefficients.
- Dimensional inspection: During the manufacturing process, dimensional inspection is carried out to check the size, shape, and position of the components on the substrate.
- Thermal management: Thermal management techniques are employed to minimize the effect of thermal expansion on the circuit’s dimensional stability.
- Stiffener placement: Stiffeners, which are rigid materials placed on the flexible substrate, are used to provide additional support and ensure dimensional stability.
Overall, dimensional control of flexible circuits is crucial to ensure that the final product meets the required specifications and functions properly.
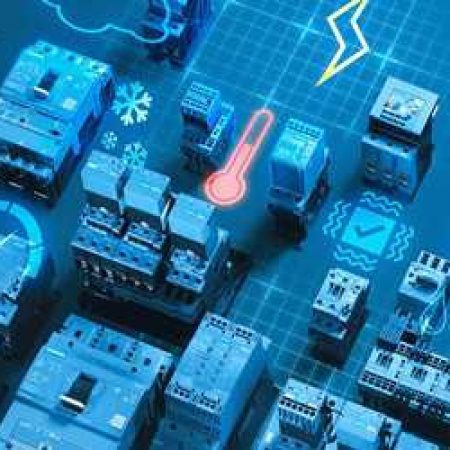
Image 3: Dimensional control
Other methods used for dimensional control of flexible circuits include:
- Adhesive selection: The type of adhesive used to attach the components to the substrate can affect the dimensional stability of the circuit, so careful selection is important.
- Tension control: During the manufacturing process, the tension applied to the substrate can affect its dimensions, so tension control is necessary.
- Laser cutting: Laser cutting is a precise method of cutting the flexible circuit and helps maintain its dimensional accuracy.
- Panelization: Panelization involves placing multiple copies of the flexible circuit on a single substrate, which helps ensure consistency in size and shape across all copies.
In addition to ensuring dimensional control during the manufacturing process, it is also important to consider the potential for dimensional changes during use. Flexible circuits can experience changes in size and shape due to factors such as temperature, humidity, and mechanical stress. Designers and engineers must take these factors into account when designing the circuit and selecting materials to ensure that it continues to function properly over time. Overall, dimensional control of flexible circuits is a critical aspect of their design and manufacturing, and careful attention to this aspect can help ensure their reliability and functionality.
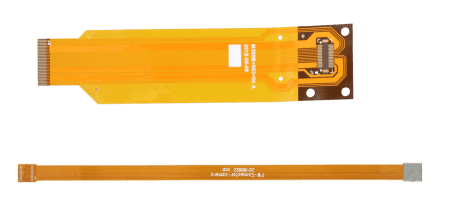
Image 4: Flex PCB by XPCB Ltd
XPCB Limited simplifies the PCB process for you. With our quick-turnaround prototyping and turnkey PCBA services, we ensure that your projects move forward smoothly and efficiently. Trust our commitment to quality and timeliness as we help you bring your designs to life. Choose XPCB Limited for a hassle-free PCB experience.